
Hopefully others with more knowledge than me (Barton?) will step in to fill in the gaps, make corrections, generally take me/us to school.
Boost Control
So first, let's clarify what we're talking about. Boost control is a method of ensuring the turbo doesn't make more boost/pressure than either is within the efficiency of the turbo, or within the limits of the car (engine or driveline), or simply to match the goals of the user.
We can control boost in a variety of ways, wastegate, manual boost controller (MBC), or electronic boost controller (EBC).
Wastegate
Wastegate is effectively non-user adjustable boost control. The turbo has a wastegate that will allow exhaust gasses to bypass the turbine wheel. When the exhaust gas goes through the turbine, it spins the connected compressor wheel and makes boost. If you bypass the turbine, the compressor spins slower and makes less boost (it depends how effective the wastegate piping is, some gas will still hit the turbine, so you will likely continue to make some boost). The wastegate sees boost pressure by a vacuum hose connected to it from the intake pre-throttle body.
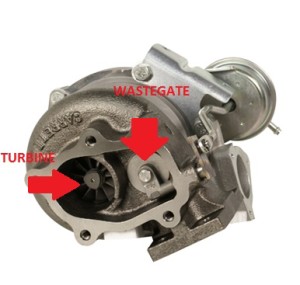
An example of an internally gated turbo

An externally gated setup
Wastegates can be internal to the turbo, or externally plumbed off the intake manifold, typically MX-5s will use an internal wastegate due to space constraints - external wastegates require additional plumbing. Traditionally external wastegates are more efficient at diverting gasses, but modern internally gated turbos are much improved over earlier versions. Wastegate's have an actuator which is what actually sees the boost pressure and will open/close the gate. The actuator has spring in it, and will fully open the gate at a certain pressure dependent on the strength of the spring, effetely with no other means of control your turbo will only make as much pressure as the wastegate spring can hold.
Note, the wastegate will begin opening at lower pressures letting more gas through the wastegate as boost pressure increases, this isn't good for an efficient spool up. In some wastegates you can swap the springs to the strength you desire. The spring pressure of your wastegate is the lowest boost your turbo will make.
Manual Boost Controller (MBC)
An MBC is a valve put between the intake (pre-throttle body) and the wastegate, it limits how much boost the wastegate spring will see. It typically has an adjustment knob, and inside is a spring.
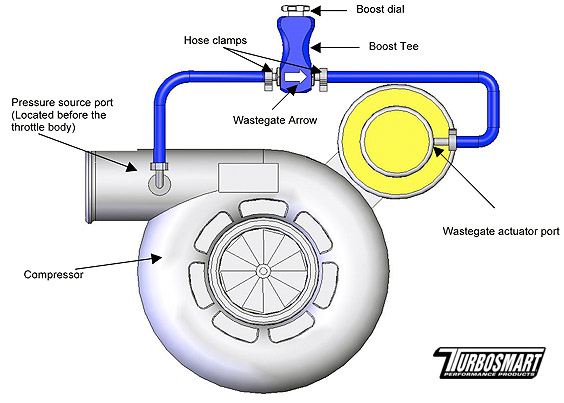
A basic routing of an MBC
Think of MBC as a wastegate before the wastegate, it's spring will control how much pressure goes to the wastegate, and how much is vented to atmosphere. If the intake is seeing 15psi, and the MBC diverts 10psi to atmosphere, the wastegate will only be seeing 5psi. This way you can run your turbo at a higher boost pressure than the wastegate spring would otherwise allow for.

A Turbosmart MBC
The adjustment knob can be used to divert more or less pressure (up to a point). It's trial and error to set an MBC, start with it fully open, see how much boost you make, then close it a click at a time until you make your desired boost/power. The turbo will make peak boost at peak engine efficiency, so you need to adjust the MBC for this point. Before and after the engine's peak efficiency boost will be lower. MBC does not allow for continuous adjustment with throttle/rpm, it's set and forget, as the name suggests, you manually make the adjustment.
Like the wastegate the spring will open at lower pressures, allowing some boost through to the wastegate before it is fully open.
Electronic Boost Controller (EBC)
EBC is a computer/controller that triggers an electronic solenoid which goes inline as the MBC did. Like the MBC it can either let air through to the wastegate, or vent it to atmosphere.

An EBC solenoid
The solenoid can be activated at various frequencies, opening and closing (pulsing) the valve to vary the volume of air sent to the wastegate. The more time spent closed the more boost is diverted from the wastegate resulting in higher boost from the turbo, the more time spent open the more air goes to the wastegate limiting the boost achieved.
By default you want the open valve to send air to the wastegate so in failure the turbo will be relying solely on the wastegate. The alternative is in failure the wastegate sees no boost and does not open at all, the turbo will make as much boost as it possibly can and likely cause catastrophic damage.
The advantage of EBC is that the we can prevent the wastegate from seeing any air until we hit our desired boost, then we can keep boost at the level we want it. There is no slow bleeding of boost as we get closer as with MBC or pure wastegate. This allows the turbo to spool faster! We can also control how much boost the turbo makes at varying RPM. For example, when the engine passes it's peak efficiency and torque begins to drop, we can use EBC to increase boost and keep the torque up.
Special note
Most ECUs will have a boost limit, even a stock ECU, that will cut ignition or fuel when a specific boost level is reached. This is a protection mechanism to prevent the previously mentioned catastrophic failure. If you have an aftermarket ECU, you should ensure this is enabled and set only slightly higher than your target boost level.